CONSULTANCY SERVICES
-
- KNOW HOW for MIG/MAG/SAW Wire Production.
- SAW Flux Production.
- Technology Transfer – Formulation for E 6010, E7010, E8010, E6013, E7018, E8018, E10018, CI, HARD FACING
- Project Management.
- Manpower Training.
- Design & Know How for making Welding electrode manufacturing machinery.
- Design Know How for Precision layer winding machine.
- Manufacturing Know How for MIG/MAG/SAW wire production with 1 year shelf life.
- Design for wire cutting machine.
- Design of Co-axial electrode Extrusion line, like EP-10(CEP-101), CEP – 141, EP -12. etc.
Other Services
- Cylinder liner
- Die head spider
- Flux cone
- Main wire guide tube, rear
- Main wire guide tube front
- Wire guide supporting tube
- Centering device
- Cap
- Coating die holder
- Nib holder
- Wire nib
- Conical wire nib (TC)
- Cylindrical wire nib (TC)
- Extrusion dies (TC)
- Wire feed roller
- TC knurled ring
- Wire guide inlet
- Wire guide centre
- Wire guide exit
- Flux cylinder Liner
- Centre shaft
- Sleeve for centre shaft
- Piston
- Ram head
- All type of rubber belts
- Emery sleeve
- Wire brush
- ‘V’ grooved rubber belt
- Sponge roller
- Leather belts
Centre shafts are made for fine grained steel for best hardness & Nitrided for best service live under extreme sliding friction.
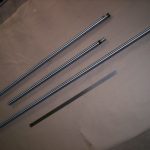
Flux stars are made from low carbon alloy steel, machined to close tolerance for best accuracy and concentricity. For best abrasion resistance the components are Carbonitrided, Hardness 60-62 RC.
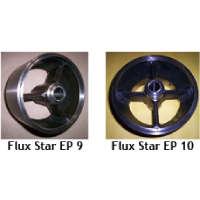
WIRE DRAWING DRUM HARD SURFACING
Base Material – Cast Iron / Alloyed Cast Iron
Proposed Process – Simple manual stick welding.
Requirement
- During Wire drawing, the draw zone is subject to metal to metal abrasion and under extreme Compressive load.
Present Method
- Wire drawing drums are Tungsten Carbide Coated. This is costly, require special skill and equipment.
New Method
- The drawing zone is welded with stick electrode. The weld deposit is rich in Chromium Carbide along with other Carbides. Resultant deposit is very hard & Wear Resistant.
- Weld deposit can be 3mm to 6mm single layer.
- Hardness 58 Degree – 60 Degree RC after two layer.
- No Relief Check(Cobweb cracks)
- Machining through grinding.
- Much cheaper than TC & other known coatings.
Alloy Basis – C, Cr, Mo, V, Ni, Mn, Si